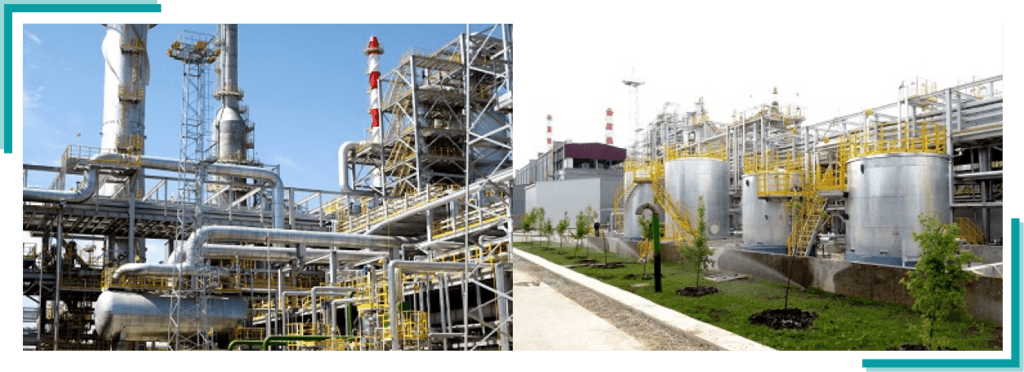
The Shymkent Refinery is the model of successful partnership of two national operators KazMunayGas and CNPC.
In parity management, an indicator of mutually beneficial cooperation is a successful execution of the tasks set before the staff of PetroKazakhstan Oil Products LLP and general contracting organization CPECC – China Petroleum Engineering Construction Corporation on completion of the large-scale project “Shymkent Refinery Modernization and Revamping”, which was aimed at fuel quality improvement to K-4 and K-5 standards, environmental safety of production, building-up of the Refinery design capacity to 6 million tons per year, as well as increase of output of light oil products for meeting the demands of the Kazakhstan market.
Modernization of the Shymkent Refinery was implemented within the framework of the State program of industrial and innovative development and has become one of the milestone events of industry and Kazakhstan in 2018.
Financing of the large-scale project was provided from the parity loans by KazMunayGaz – PM JSC and CNPC E&D. Also, the loan was received from “Development Bank of Kazakhstan” JSC. The sum of project implementation investments was 1.8 billion US dollars.
Considering the fact that the Refinery provides about 30% of the total output volume of oil products in Kazakhstan, one of the main conditions was performance of all work without stopping the main production. The professional team managed to complete the Project successfully within the established deadline.
It is to be reminded that the “Shymkent Refinery Modernization and Revamping” project was implemented in two stages. The general contractor was CPECC company (China Petroleum Engineering and Construction Corporation), a subdivision of CNPC corporation, possessing a wide experience in implementation of large investment projects worldwide.
The following units were commissioned upon completion of the first stage: Light Naphtha Isomerization Unit, Sulfur Production Unit with capacity of 4.0 tons per year, revamped Diesel Hydrotreatment Unit, and Automated On-spot Loading Unit.
The following units were commissioned at the second stage: Catalytic Cracking Complex with capacity of 2.0 million tons per year; Catalytic Cracking Gasoline Hydrotreatment Unit with capacity of 1.0 million tons per year; Unsaturated LPG Desulfurization Unit with capacity of 303.1 thousand tons per year; Alkali Treatment Unit with capacity of 6,0 thousand tons per year; Saturated LPG Desulfurization Unit with capacity of 145.0 thousand tons per year; Sulfur Production Unit with capacity of 15.0 thousand tons per year; C3/C4 Splitter with capacity of 301.9 thousand tons per year; Amine Recovery Unit with capacity of 1.345 thousand tons per year; Sour Water Stripper with capacity of 792.1 thousand tons per year; and Pressure Swing Absorption Unit with capacity of 209.8 thousand tons per year. Also, the CDU of LK-6U complex with capacity of 6.0 million tons per year was revamped.
Thus, upon completion of the Project the volume and the slate of output products have increased.
The works on modernization of the Refinery treatment facilities were completed. Use of “enclosed” and “ground” equipment prevents emissions into the atmosphere and soil cover, and allows saving fresh water to 1.5 million m3 per year. The reduction in emissions of hydrocarbons and other polluting substances into the atmosphere up to 90 %, and reduction in saturated/unsaturated hydrocarbons up to 21 % have been achieved.
Also, the containers for collection of the used power sources and plastic boxes for waste paper collection were installed at the enterprise, according to the requirements of article 288 of the RK Environmental Code and according to “Rules of organization of collection, storage, utilization and removal of wastes of production and consumption”.
One thousand tones of oil sludge was removed for processing and disposal. Within the frames of landscaping and improvement of the territory, many young plants of various bushes and trees were planted at the enterprise. Solar panels with a total area of 350 sq.m and 10 wind generators were installed. Also, the enterprise created the conditions for movement along the sites using the ecological transport – by bicycles and electromobiles.
With commissioning of the new units, PKOP LLP conducted additional certification of 284 new workplaces in 2017-2018. It should be noted that 98 % of the Refinery staff are the citizens of Kazakhstan, and only 2 % are foreign citizens.
Moreover, 4,800 local workers with attraction of 30 companies of Shymkent city and Turkestan oblast were involved during the project implementation period.
Within the frames of mutual experience exchange, the trip to the Chinese refineries and the industry enterprises of the People’s Republic of China is organized annually for the staff of the company.
For high performance indicators in creation of safe working conditions to employees of the enterprise, PetroKazakhstan Oil Products LLP was awarded with a special diploma and a cup of prize-winner in contest “Model Safe Enterprise”, organized on the occasion of “World Day of Labor Protection”.
The management and the staff of PetroKazakhstan Oil Products LLP were awarded with the State awards, medals and certificates of honor for achievements in productive activity and contribution to implementation of the “Shymkent Refinery Modernization and Revamping” project.
So far, PKOP LLP widely uses the international experience in the field of advanced new technologies, digitalization, and improvement of production processes, which has been made possible primarily owing to effective and fruitful cooperation at the level of national operators of Kazakhstan and China.