official website
PROTECTION OF ATMOSPHERIC AIR
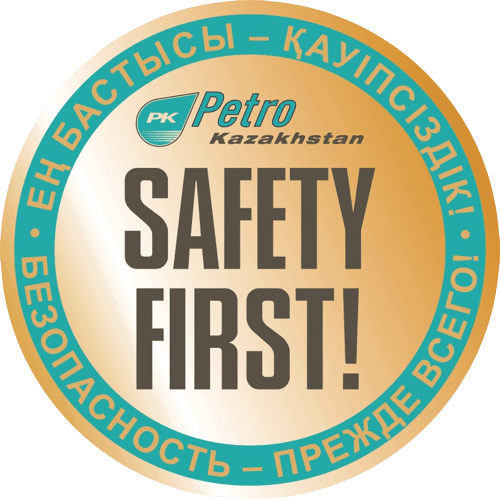
Within the frames of the State Program for Industrial and Innovative Development of the Republic of Kazakhstan for YY2015-2019, the construction of new process units was completed at PKOP LLP. Commissioned facilities have an environmental effect aimed at reducing the environmental emissions.
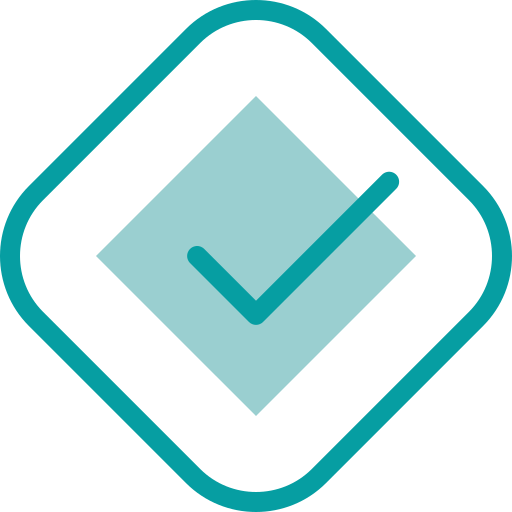
In July 2017, the isomerization unit was launched with the output of fuel of К4 and К5 classes. When using fuels of К4 and К5 classes, emissions of sulphur dioxide to the atmosphere are reduced; it leads to improvement of the environmental situation in the region as a whole.
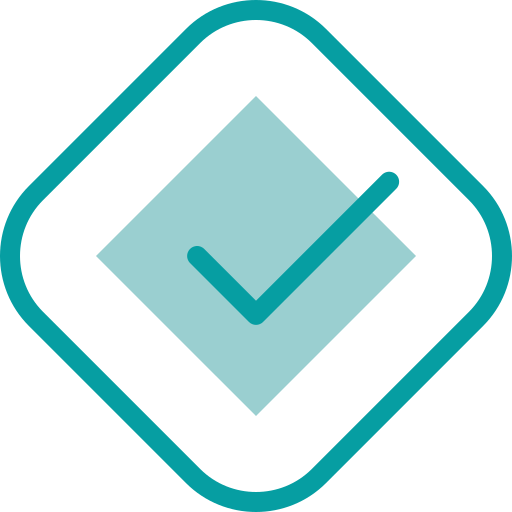
A Wet Flue Gas Scrubber (Flue Gas Combustion) System (BELCO) is available at the RFCC Heavy Residue Catalytic Cracking Unit (1,000) with a capacity of 2,000 thousand tpa on the flue pipe DO -1014 (Wet Gas Scrubber). BELCO’s EDV waste gas wet cleaning technology is designed to reduce particulate matter and SOx in emissions of catalytic cracker with treatment coefficient of 98%.
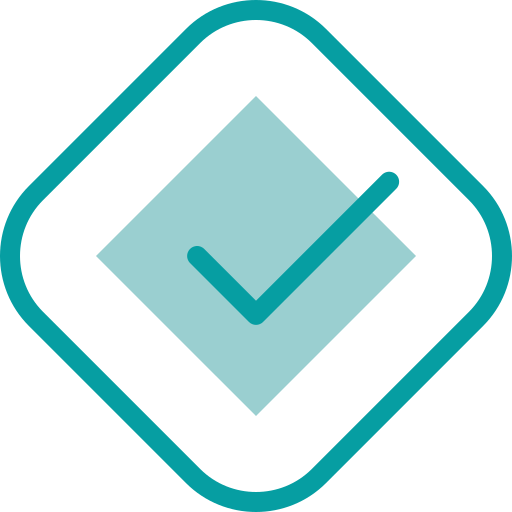
Tank farms (tit. 3600) were built taking into account the reduction of limit hydrocarbon emissions, as they are equipped with a floating roof and a nitrogen cushion which captures vapour emissions by 95%. A line is provided for for pump units to return product to the tank farm with the installation of a control safety valve to maintain a minimum flow.
The entire technological process is ensured by strict observance of the process mode, with prevention of environmental incidents and compliance with technological control norms specified by the technological instructions and technological regulation.
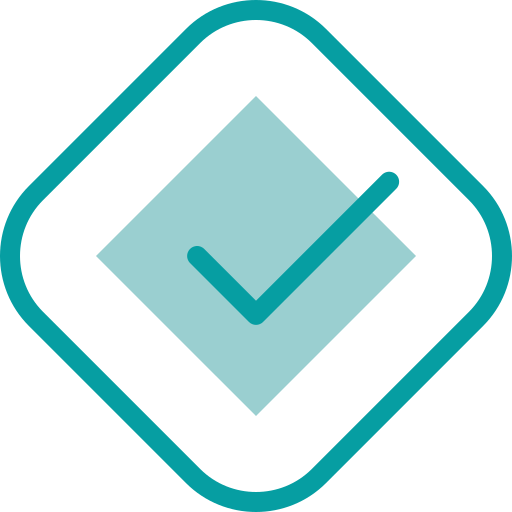
The sulfur production unit with a capacity of 4 thousand tons per year was put into operation. The unit is aimed at utilization of acid gases previously burned on a flare, with the production of sulfur with a purity of more than 99.9% by weight. In connection with the commissioning of SPU-4000 tn. emissions of sulphur dioxide (SO2) into the atmosphere decreased by 21%.
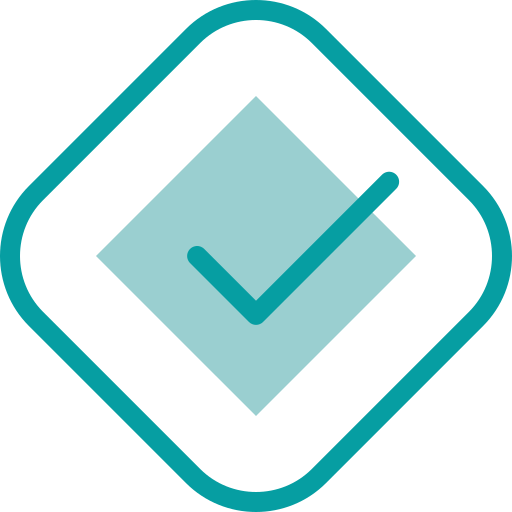
Within the frames of the 2 stage of modernization, SPC (sulphur production complex) with a capacity of 15,000 tons/year was put into operation. The unit is aimed at utilization of acid gases previously flared with the production of pure sulfur with a content of 99.9 wt%. Due to commissioning of the SPC, emissions of sulphur dioxide (SO2) into the atmosphere decreased by 48%. Due to commissioning of the SPC, emissions of sulphur dioxide (SO2) into the atmosphere decreased from 1,476 tons. up to 710 tons.
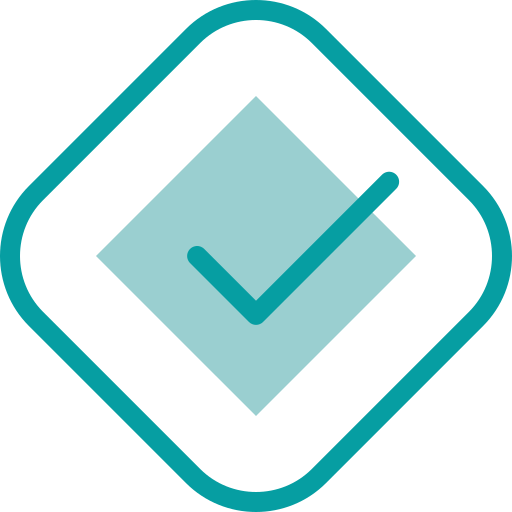
Oil-products on-spot loading unit was put into operation in CTG. Emissions of volatile hydrocarbons into the atmosphere during filling decreased upon commissioning of the Light oil-products On-spot loading. The proportion of volatile hydrocarbons decreased by 7%.
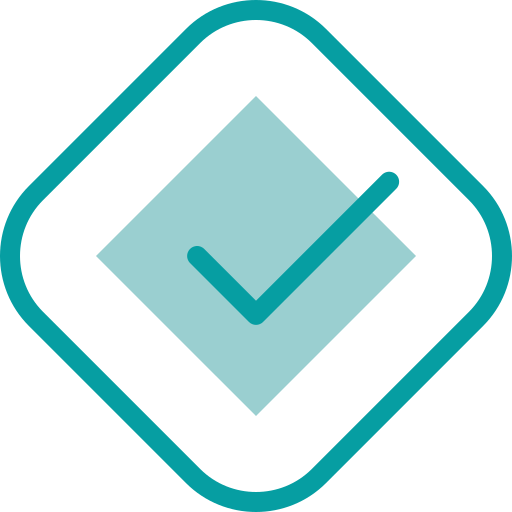
In order to reduce discharges of oil products with drainage water and improve the operation of the enterprise’s sewerage networks, a pilot version of an automatic drainage system has been introduced with an integrated system of preliminary separation of tank drainage waters into a hydrocarbon component and water, which has proven itself on the positive manner.
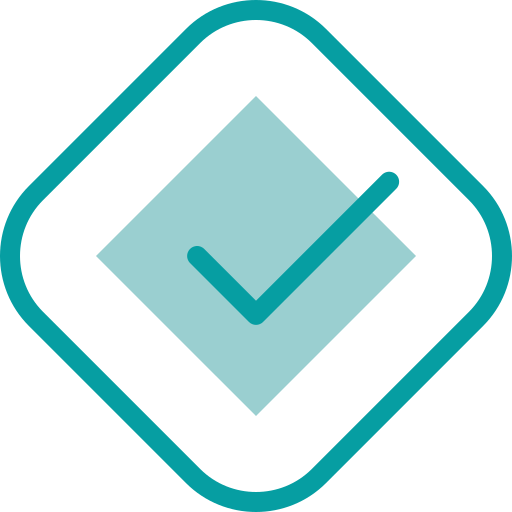
Within the frames of the modernization, new treatment facilities were put into operation. This led to increase in the capacity of the Refinery’s treatment facilities and improvement in the quality of wastewater treatment.
Additional treatment of effluents at the reverse osmosis unit saves fresh water up to 1.5 million m3 per year. The erected equipment is sealed, which allows to reduce emissions of pollutants and stench into the atmosphere. Upon removal of pollutants to the deodorization unit. Upon introduction of new sealed facilities, emissions of limit and unsaturated hydrocarbons from the Refinery’s treatment facilities decreased by 17%.
Due to completion of the work on the modernization of treatment facilities, the efficiency of treatment of industrial wastewater for oil products and suspended substances was improved from 76% to 98%, which reduces the environmental burden by reducing emissions to the environment.
Specific emission of pollutants at PKOP LLP:
Oil-refining, t/1,000 t. of crude oil processed | 2020 | 2021 | 2022 |
---|---|---|---|
2,2 | 2,98 | 3,38 |